The Importance of Positive Displacement Pumps in Industrial Applications
Positive displacement pumps are crucial components in various industrial processes, renowned for their ability to move fluids at consistent rates regardless of the system pressure. These bombas de desplazamiento positivo industriales are revered for their precision, efficiency, and the broad range of materials they can handle. From food processing to pharmaceuticals, chemical manufacturing to waste management, positive displacement pumps are indispensable.
Understanding Positive Displacement Pumps and Their Mechanism
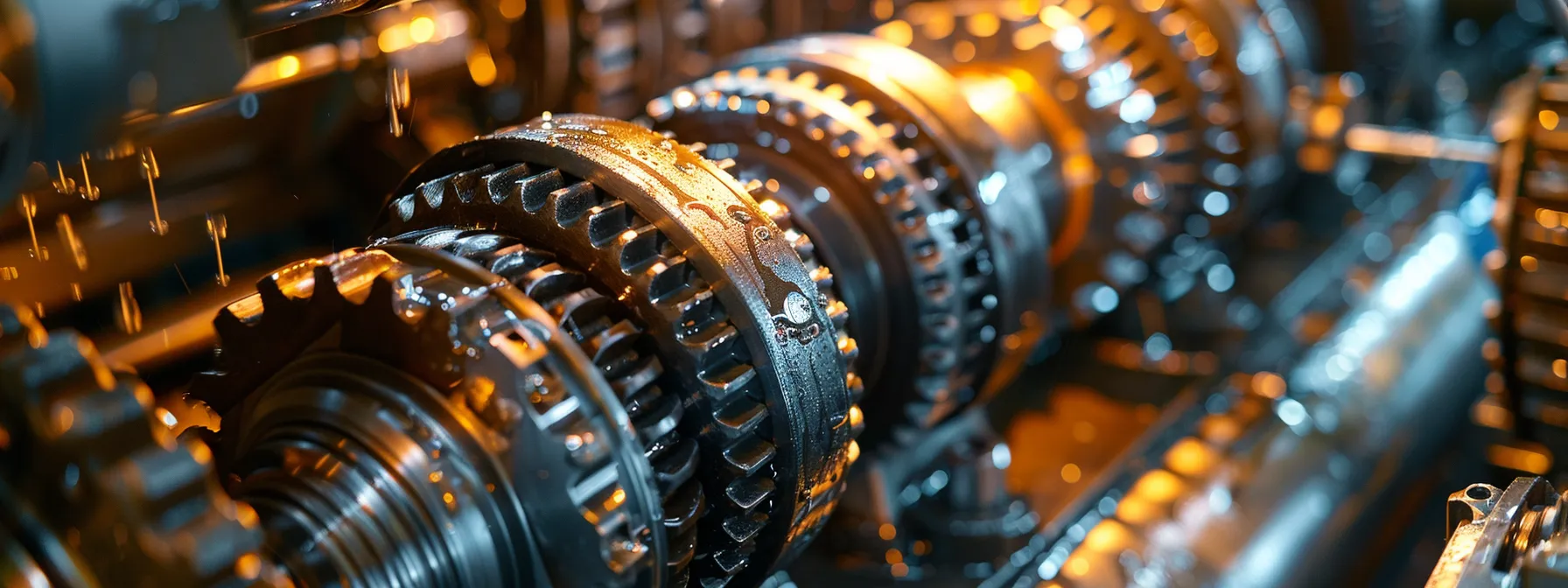
At the core of positive displacement pumps is their ability to trap a fixed amount of fluid and force it through the pump’s discharge. Unlike centrifugal pumps, they operate by mechanically enclosing a volume of fluid and conveying it to the pump outlet, resulting in a direct flow irrespective of the external pressure conditions. This accuracy in flow rate is instrumental for applications that demand exact dosing or substance displacement.
Positive displacement pumps come in various designs, each tailored to specific tasks. The most common types include gear pumps, diaphragm pumps, and piston pumps. These different configurations efficiently handle various fluids, ranging from highly viscous to those containing large solids, each with functionality that matches industry requirements.
The precise operation of positive displacement pumps is facilitated by internal components designed for minimal leakage and maximum volumetric efficiency. This mechanism ensures a consistent performance even with the presence of more viscous fluids or at higher pressures. The intricate design and engineering of these pumps significantly contribute to their overall efficiency and reliability.
Maintaining their condition is crucial, and bombas de desplazamiento positivo industriales are built to withstand the stressors of heavy-duty applications. With robust materials and user-serviceable parts, industrial positive displacement pumps are meant for endurance, equipped to deliver precise flow under demanding operational conditions while minimizing downtime and maintenance needs.
Versatility of Positive Displacement Pumps in Various Industries
Positive displacement pumps are exceedingly versatile, finding their way into various industrial operations. Their aptitude for managing a diverse array of fluids makes them suitable for various sectors. In the food and beverage industry, for instance, they handle everything from thick pastes to delicate wine transfers, managing the process with gentle efficiency and without damaging the product.
The pharmaceutical industry benefits greatly from the exacting nature of positive displacement pumps. The need for strict control over dosing and the sanitary handling of fluids is non-negotiable when producing medicines and other health-related products. These pumps offer the necessary precision and cleanliness, often being constructed with materials that are easy to sterilize and maintain.
Processing chemicals is another area where positive displacement pumps excel. They can withstand corrosive or abrasive substances, move them safely, and maintain constant flow rates, which are essential for consistent quality and safety in chemical manufacturing. Even industries that work with sludges and waste rely on these pumps for their ability to handle high-viscosity fluids laden with solids.
In oil and gas operations, the pumps play a pivotal role in transfer tasks, both in upstream and downstream processes. Whether for drilling mud, hydrocarbons, or refined products, positive displacement pumps are engineered to handle the rigors and safety requirements of the energy sector. Their resilience and steadfast operation make them an industry favorite.
The Role of Positive Displacement Pumps in Ensuring Process Efficiency
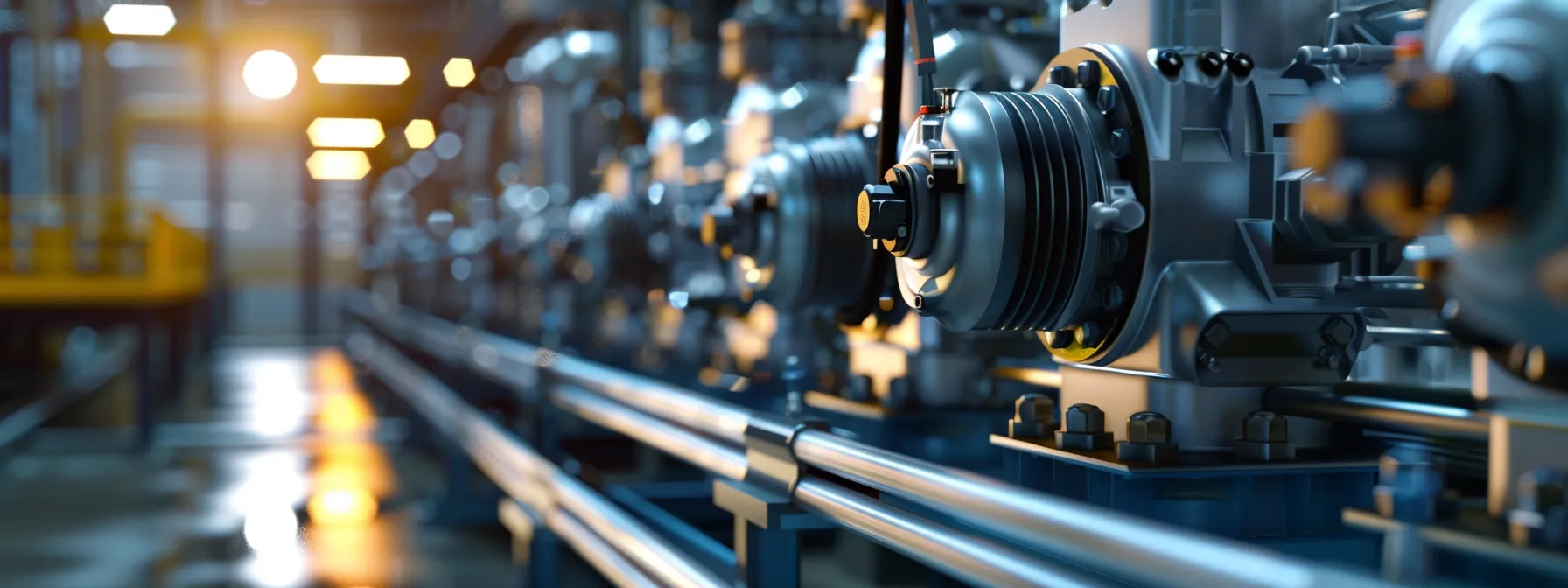
In an industrial landscape where efficiency and precision are paramount, positive displacement pumps are not just beneficial but often necessary. Their defined fluid displacement ensures an accurate volumetric flow rate, which is key for many manufacturing processes. This precision leads to significant improvements in overall process efficiency, allowing for streamlined operation, reduced waste, and higher quality outcomes.
Energy efficiency is another critical factor in their favor. Since positive displacement pumps cause less friction loss compared to other pump types, they require less power to move a given volume of fluid. This translates to lower operational costs and a smaller carbon footprint, an aspect increasingly important in today’s energy-conscious market.
The consistent pressure and flow provided by these pumps can prevent the need for additional metering pumps and control systems, simplifying the process setup. By reducing the complexity of fluid movement workflows, industries can cut down on potential failure points and maintenance requirements, optimizing their operations for longevity and reliability.
Furthermore, the adaptability of these pumps to fluctuating system pressures without compromising their performance enhances process stability. This stability is crucial for industries that rely on continuous production cycles and that cannot afford inconsistencies or interruptions due to pump failures or malfunctions.
Overall, the many benefits of positive displacement pumps in industrial applications solidify their status as vital components in process efficiency, system reliability, and economic operations. Their precise fluid handling capabilities and robust construction make them essential in various sectors, contributing to the continued innovation and productivity of industries worldwide.